Certificates
Bearings Care
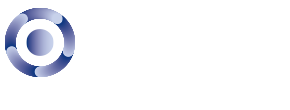
Sign up for our newsletter to stay up-to-date with our promotions, discounts, sales, and special offers.
subscription
navigation
Categories
- Deep Groove Ball Bearing
- Ball Screw
- Self-aligning Ball Bearing
- Spherical Roller Bearing
- Thrust Aligning Roller Bearing
- Tapered Roller Bearing
- Thrust Ball Bearing
- Angular Contact Ball Bearing
- Thrust Roller Bearing
- Cylindrical Roller Bearing
- Pillow Block Bearing
- Machinery Equipment
- Thrust Conical Roller Bearing
- Bearing Cage
- Discount and Promotion all bearing
- Steel Balls
Contact Person
- Name:
- Summer Sun
- Tel:
86-0411-88700549
- WhatsApp:
- https://wa.me/8618804285329
- Address:
- No.120 Jinma Road, Dalian Economic And Technological Development Zone, Dalian, Liaoning, China (Mainland)

Email: Click to contact me
Friend Links: