What to Do with Bearing Noise Caused by Manufacturing Factors?
What to Do with Bearing Noise Caused by Manufacturing Factors?
Causes of bearing noise
From the perspective of the bearing industry, working conditions can be solved by putting forward reasonable requirements for the host. And how to reduce the vibration and noise caused by manufacturing factors is a problem that the bearing industry must solve.
A large number of tests have shown that the machining quality of cages, ferrules, and steel balls has varying degrees of impact on bearing vibration. Among them, the machining quality of steel balls has the most obvious impact on bearing vibration. It is followed by the machining quality of ferrules, which is the most important. The factors are the roundness, waviness, surface roughness, surface bumps, etc. of the steel ball and ferrule.
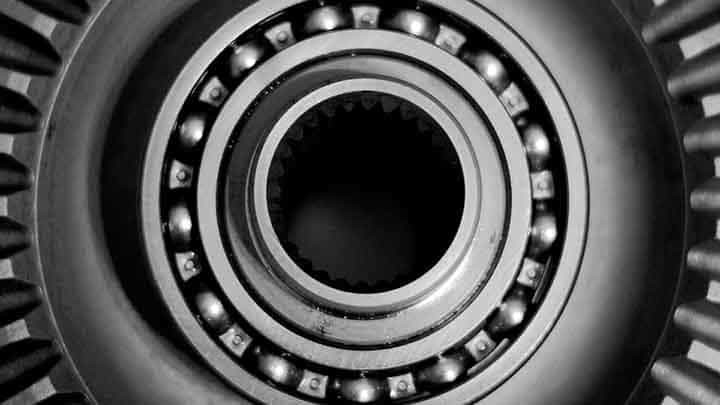
For steel ball products
For ferrule products
How to reduce bearing noise by avoiding random bumps?
The first point
To reduce the vibration of the rolling surface during ultra-precision grinding, and obtain good surface processing shape accuracy and surface texture quality. To reduce vibration, the grinding machine must have good vibration resistance. And important structural parts such as the bed have vibration absorption.
The oilstone oscillation system of the precision machine tool has good anti-vibration performance; it improves the grinding speed.
In high-speed grinding, the grinding force is small, the degraded layer is thin. So it is not easy to burn, and the machining accuracy and efficiency need improving, which has a great impact on low-noise ball bearings. The dynamic and static stiffness of the spindle and its speed characteristics also have a great impact on low-noise ball bearings. Grinding vibration has a great influence.
The higher the stiffness, the less sensitive the grinding speed to changes in grinding force. The smaller the vibration of the grinding system as well. The rigidity of the spindle bearing support receives improving. And the random dynamic balance technology is adopted to improve the vibration resistance of the grinding spindle.
The second point
Improve the accuracy of the machining reference surface and reduce the error in the grinding process. The outer diameter and end surface are the positioning benchmarks in the grinding process. So the error reflection of the outer diameter to the groove super-precision is this indirectly transmission through the outer diameter to the groove grinding. And the error reflection of the groove grinding to the groove super.
If the workpiece bumps during the transfer process. It will be directly reflected on the surface of the raceway, which will affect the vibration of the bearing. Therefore, the following measures must be necessary: improve the shape accuracy of the positioning reference surface; smooth transmission during the processing process without bumps. The shape and position error of the blank remaining amount should not be too large.
Especially when the remaining amount is small, the excessive error will cause the final grinding and super precision. In the end, the shape accuracy has not been improved to the final quality requirements, which seriously affects the consistency of processing quality.